|
9月8日(月)から9月12日(金)にかけて、ドイツ・トラベミュンデで開催された第11回超伝導応用国際会議(Workshop on RF Superconductivity, SRF-2003)において、樋口玉緒氏が、若手研究発表(20分のオーラル)最優秀賞(初代)を受賞しました。
樋口氏は、今年3月「新しい機械研磨と電解研磨による水素吸蔵を起こさない超伝導空洞の表面処理法の開発」で総合研究大学院大学(総研大)博士号(工学博士)を取得しました。その内容を発表したもので、研究のオリジナリティー、超伝導空洞業界への多大な寄与(簡単、低コストの表面処理)が高く評価されました。
同氏の研究略歴
- 1994年3月 立命館大学大学院・理工学研究科・物理学専攻・博士課程前期課程終了。理学修士。
- 1994年4月 株式会社 野村鍍金入社。
- 1994年5月より2年間KEK受託研究員として超伝導空洞の表面処理の研究に従事。
特に、ニオブ空洞の内面機械研磨として簡便なバレル研磨の開発を行う。
|
|
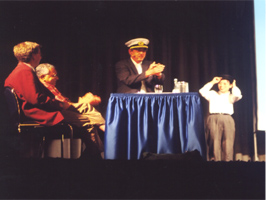 |
- 1997年4月 株式会社野村鍍金鹿沼工場でニオブ加速空洞の電解研磨及び化学研磨等の表面処理技術業務につく。
- 1999年4月、高速バレル研磨の開発のためKEKの要請を請け、再度KEK受託研究員。一貫した研究活動のために、同年、9月総研大を受験、合格。
- 2000年4月〜2003年3月会社在籍のまま、社会人学生として総研大在学。遠心バレル研磨の開発、電解研磨での水素吸蔵に関する研究に専念。
- 2003年3月 「新しい機械研磨と電解研磨による水素吸蔵を起こさない超伝導空洞の表面処理法の開発」の研究で総研大・博士号(工学博士)を取得。
- 2003年9月 SRF2003での若手研究者発表最優秀賞(初代)を受賞。
SRF2003での発表内容
総研大での博士研究結果として、SRF2003で「水素フリー電解研磨と水素吸蔵現象について」の題目で超伝導ニオブ加速空洞の表面処理に関する発表を行った。発表の内容は以下の通りである。
超伝導加速空洞の大規模実用化は1989年にKEKに建設されたTRISTAN超伝導空洞で初めて成功した。この成功以後、超伝導加速空洞が各国の研究所で電子・陽電子衝突型のストレージリング、FELなど広く用いられるようになった。次世代の超伝導加速空洞の大規模応用として、例えばTESLA(TeV Energy Superconducting Large Accelerator)がある。TESLAでは25MV/m以上(従来の5倍)の高電界性能が要求される。この大規模応用では空洞の加速電界の向上と同時に空洞製作コスト削減が重要な研究課題である。特に、空洞製作面では表面処理における空洞性能の高信頼性の確保と同時に処理工程の単純化が必須である。
TRISTANは、長期運転における超伝導空洞の当時の高性能(5-10MV/m、 Qo-2x109)、高信頼性を実証した。しかし、その表面処理工程は、機械研磨(バフ研磨)、予備電解研磨(2-3μm)、電解研磨(80μm)、真空アニール、仕上げ電解研磨(10μm)と煩雑・高コストであった。ここでバフ研磨は空洞内面の表面欠陥層を強力に除去する工程であり、空洞性能の信頼性を上げるために重要な工程である。しかし、このバフ研磨では、砥粒をニオブ面に埋め込む。電解研磨液循環システムを砥粒で汚染しないように、予めその汚染を除去する必要がある。そのために、予備電解研磨が必要で、空洞内に閉じ込めた研磨液で少量電解研磨し、その汚染液を捨てる方法をとっている。電解研磨は、滑らかな表面を作るもので、当時としてはKEKのみが採用した方法である。最近では、高電界空洞にとって不可欠の技術として世界的に注目されている。真空アニールは電解研磨処理中に吸蔵された水素を除去し、水素吸蔵による空洞の性能劣化(水素病)を回復させる工程である。しかし、工業炉を使用するので空洞内表面が汚染され、表面を清浄にするために仕上げ電解研磨が必要であった。
既に述べたように、TRISTANでは機械研磨としてバフ研磨を採用した。空洞は、ハーフセルを電子ビーム溶接して製作するが、その溶接シーム部には、溶接欠陥が発生し易く、それがクエンチの原因になるので、その部分をも積極的に研磨する必要がある、しかし、バフ研磨は多セル化された複雑空洞形状に適応することが難しく電子ビーム溶接シームを一括研磨できない。つまり、空洞完成後、溶接シームは別途グラインド研磨しなければならない。そこで、一括研磨可能な簡単な機械研磨方法としてバレル研磨を開発した。この方法は、空洞内に研磨石と研磨剤(石鹸水)を空洞内に入れてガラガラ回して研磨する方法であり、時間がかかるが非常に簡便である。この方法で空洞性能が確保出来ることを確認した上で、バレル研磨の低研磨速度の克服のために、遠心バレル研磨法(公知の技術)を適用し、研磨速度の高速化に成功した。9連空洞を例にとると、バフ研磨と溶接部のグラインド研磨で3週間程度を要していたところを
1日に短縮できた。
この機械研磨の後、研磨砥粒の埋め込みや研磨カスを除去するため化学研磨或いは電解研磨(予備研磨)を施す必要がある。しかし、高電界性を確保するには化学研磨ではなく電解研磨による滑らかな表面仕上げが不可欠である。我々は機械研磨と電解研磨の組合せ処理を基本とした簡単な表面処理の開発に着手した。つまり、アニールを省くことを追求した。
始めに遠心バレル研磨と電解研磨を施し真空アニールを省いたところ、結果は著しい水素病が発生した。
次に、機械研磨を施さずにLバンド単セル空洞を横型連続電解研磨(TRISTANの方法)で200μm多量研磨し、水素病が観察されなかった。従来から電解研磨で水素吸蔵し易いことが知られているが、ここでは電解研磨は必ずしも水素吸蔵を引起すとは限らないことを突止め、更に電解研磨中、常時電圧を印加することが水素吸蔵防止に有効であることを明確にした。つまり、電解研磨では、空洞が陽極になるので、サイズの小さい水素イオン(H+)がポテンシャルバリヤーのためにニオブに侵入できない。
そこで機械研磨工程が水素吸蔵の原因と考え、サンプルを用いて水素ガス分析調査した。遠心バレル研磨で多量の水素吸蔵が起きること、バレル研磨液(水等)を構成する水素がニオブに吸蔵されることが分かった。水素を含まない溶媒(市販のフロリナート)の選択でこの水素吸蔵の問題を解決し、水素フリーの遠心バレル研磨法の開発に成功した。これが、一つ目の発明である。
この水素フリー遠心バレル研磨と電解研磨、或いは化学研磨を組合せた表面処理法をLバンド単セル空洞に適用した。電解研磨を組合せた場合には著しい水素病が発現したが、化学研磨を組合せた場合には水素病が起こらなかった。
電解研磨を組合せた場合の失敗から、機械研磨キズのあるニオブ表面が特に水素を吸蔵しやすいことが分かった。また、化学研磨を組合せた場合の成功から、酸化プロセスが水素吸蔵阻止に重要であることが示唆された。化学研磨では定常的な酸化過程とその酸化物の溶解により研磨が進行する。電解研磨では印加電圧による電気化学的な酸化過程とその酸化物の溶解により研磨が進行する。予備電解研磨では、機械研磨による表面欠陥が多数存在する状態で印加電圧がかけられない状況を経由する(研磨液注入時等)。このプロセスに於いて水素陽イオンが表面欠陥に吸蔵されることをサンプルで確認した。また、表面の機械研磨キズを除去した後では、その後の電解研磨で水素を吸蔵しない。したがって、電解研磨でも定常酸化過程を付加すれば予備電解研磨で起る水素吸蔵を防止できる可能性がある。予備電解研磨液に酸化剤である硝酸添加を試みた。ここで硝酸添加量が多いと化学研磨になり電解研磨面が得られない。硝酸添加量が少量であることが望ましい。1500ppm(研磨液4リットルに対し60%濃度の硝酸10cc)の少量硝酸添加をした電解研磨液でLバンド単セル空洞を予備研磨し、その後従来法による連続電解研磨を50μm施した。水素病は起こらず、加速電界30MV/mが達成できた。その再現性を確認できた。これが二つ目の発明である。
結論として、
- ニオブ空洞の簡便かつ高速な機械研磨法(遠心バレル研磨法)を開発した。
- この機械研磨法での水素吸蔵を調査し、水素フリー機械研磨法を発明した。
- 定常酸化プロセスを付加した電解研磨法(もちろん化学研磨でも可)で遠心バレルによる砥粒汚染層、ダメ-ジ層を水素吸蔵させることなく除去する方法を発明した。
- こうした発明の組み合わせと従来の電解研磨を採用することで30MV/mの高電界性を保証する簡単な表面処理法を確立した。
- 結果としてアニール不要で簡単な超伝導空洞表面処理法を開発した。
この開発の中で、湿式機械研磨では金属表面に研磨キズが発生する瞬間にそのキズが研磨液を構成する水素を分解・吸着・吸蔵するラジカル反応が起きることを明確にした。また、定常酸化プロセスがこのラジカルな水素吸蔵プロセスの進行を阻止するのに有効であることを見出した。
この研究成果は、超伝導空洞の表面処理を著しく簡単化するもので、TESLAのように超伝導空洞を2万台以上も製造する場合、設備投資の低減、処理時間の短縮化等大きなコストメリットを導くことは明らかである。
|
|
|